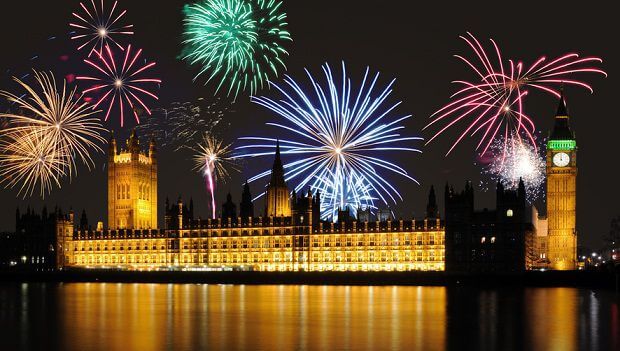
Happy New Year!
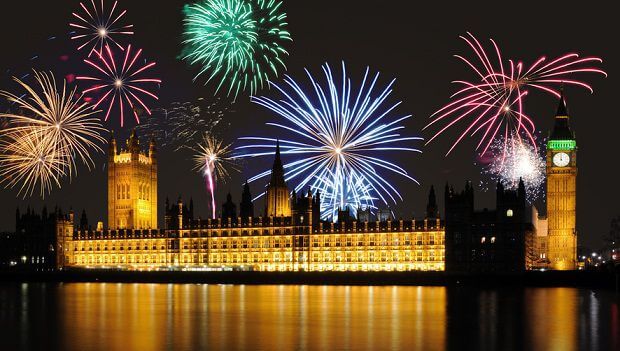
Happy New Year to you all! I so hope that it will be better for us all than 2021!
We have been busy in the workshops, and the Gibran Crime and Punishment mould has just been finished off, ready to go to the foundry. Here’s the photographic evidence!
Using the clay enlargement, we have made this resin. From that we have made a mould which can also be used ultimately to send to the foundry to cast it as a work of art – a bronze sculpture. 2023 is the centenary of the publication of Kahlil Gibran’s stupendous work ‘The Prophet‘. Perhaps it will be the year in which this heroic work is made truly public too.
The man is knocking at the gates of Heaven asking for forgiveness.
Happy New Year !
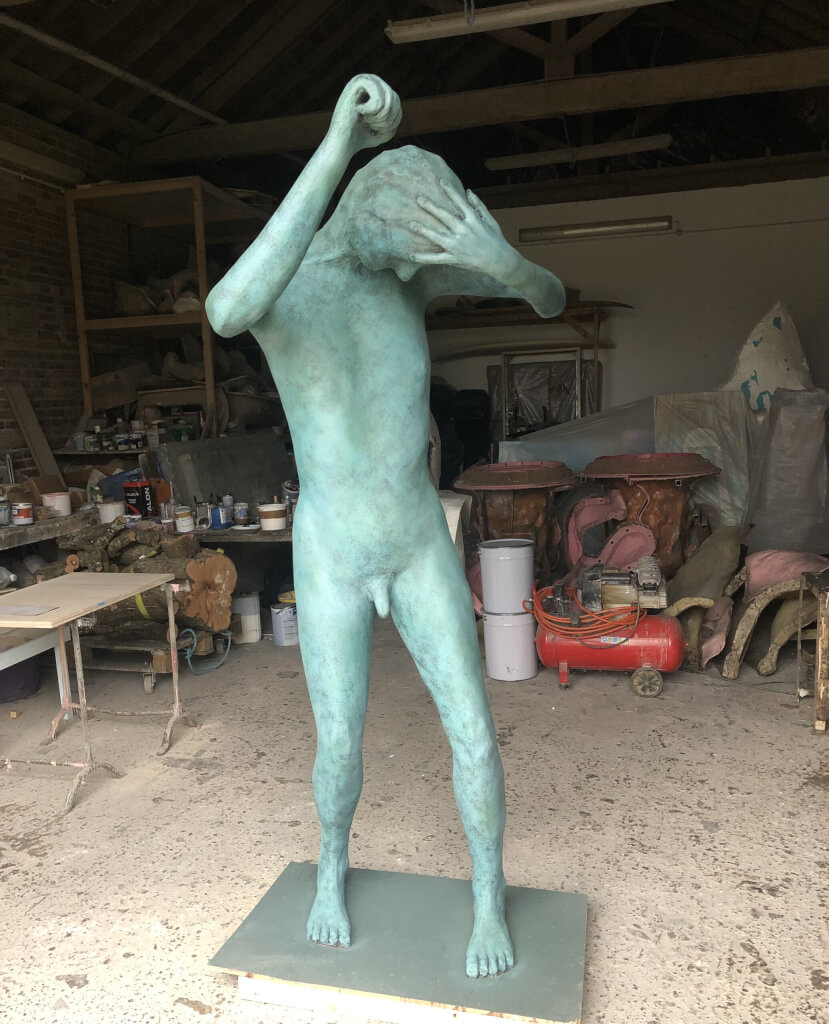
The latest photo of the finished resin for Speak to us of Crime and Punishment
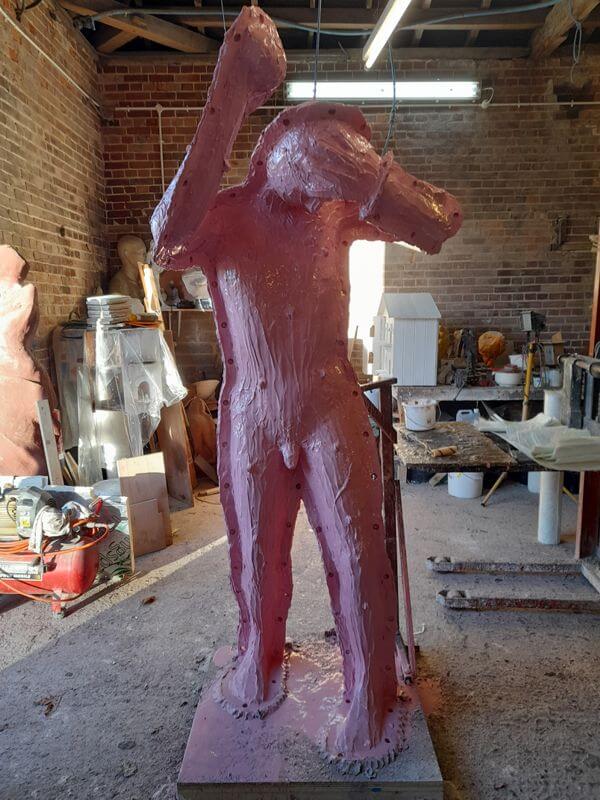
A front view of the full-sized mould for the Gibran Series sculpture, Speak to us of Crime and Punishment
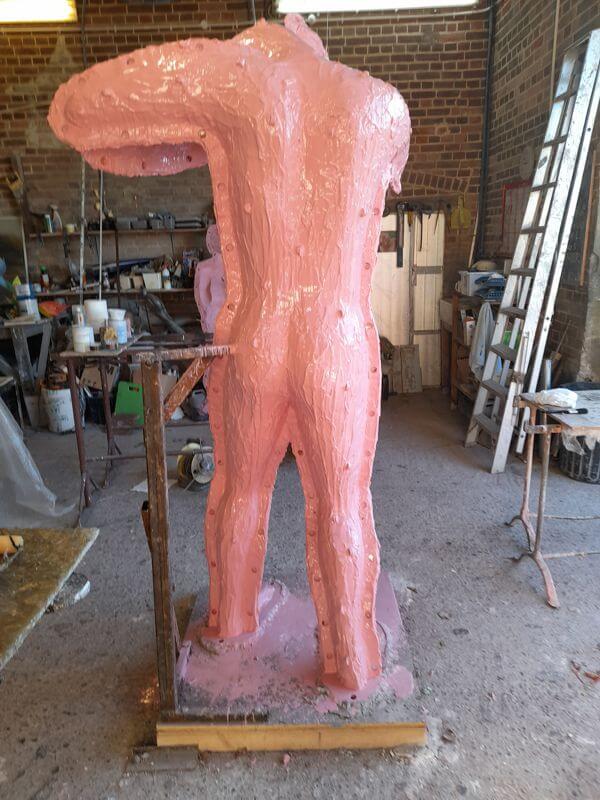
Gibran Sculpture Series – Speak to us of Crime & Punishment.
Full sized back view of mould.
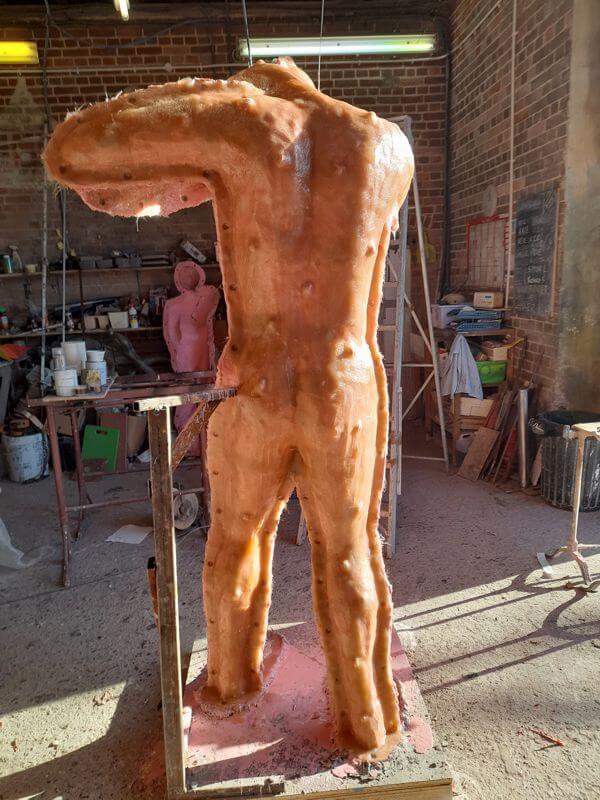
Gibran Sculpture Series – Speak to us of Crime & Punishment.
Full sized back view of mould. – in the sun!
A Very Happy New Year !
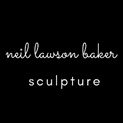
Recent Comments