The Gibran Sculpture Series
We’ve moved on to the next stage in making the large (2.2m) Speak to us of Freedom sculpture.
The mould that was made of the enlarged model has been delivered to the Talos Art Foundry. The foundry is near Andover in Hampshire and specialises in casting bronze sculpture. Now the long and complex process of taking a mould to a finished bronze begins.
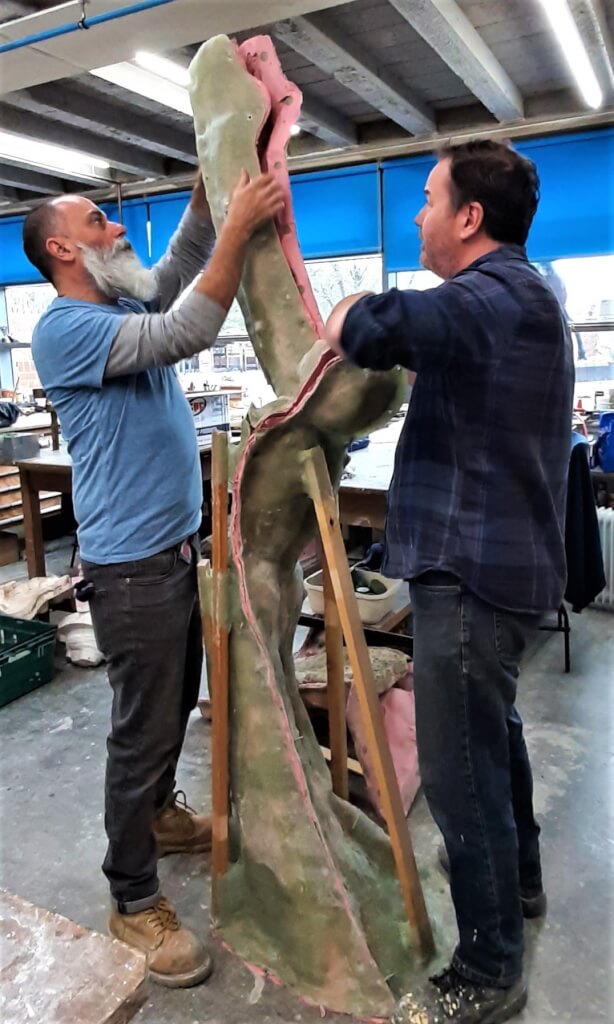
The mould has arrived at the foundry and here it is being taken apart to be ready for the next stage.
The mould is in sections and the first stage is painting wax into each of the sections. In the pictures, you can see how thick the wax is and that will be the thickness of the final bronze.
Making sure the metal flows!
Runners and risers are added to each section of the pattern. These make sure that the molten metal runs into every nook and cranny of the mould. As the molten metal flows into the mould, it solidifies very quickly. If the space it’s going into is thin, it cools even more quickly and that often means that it won’t fill the mould. So, these ‘internal pipes’ make sure that the metal runs down to the bottom of every bit and runs up to the top of every bit. Without them, air will get trapped in the mould and there will be bits missing from the finished casting.
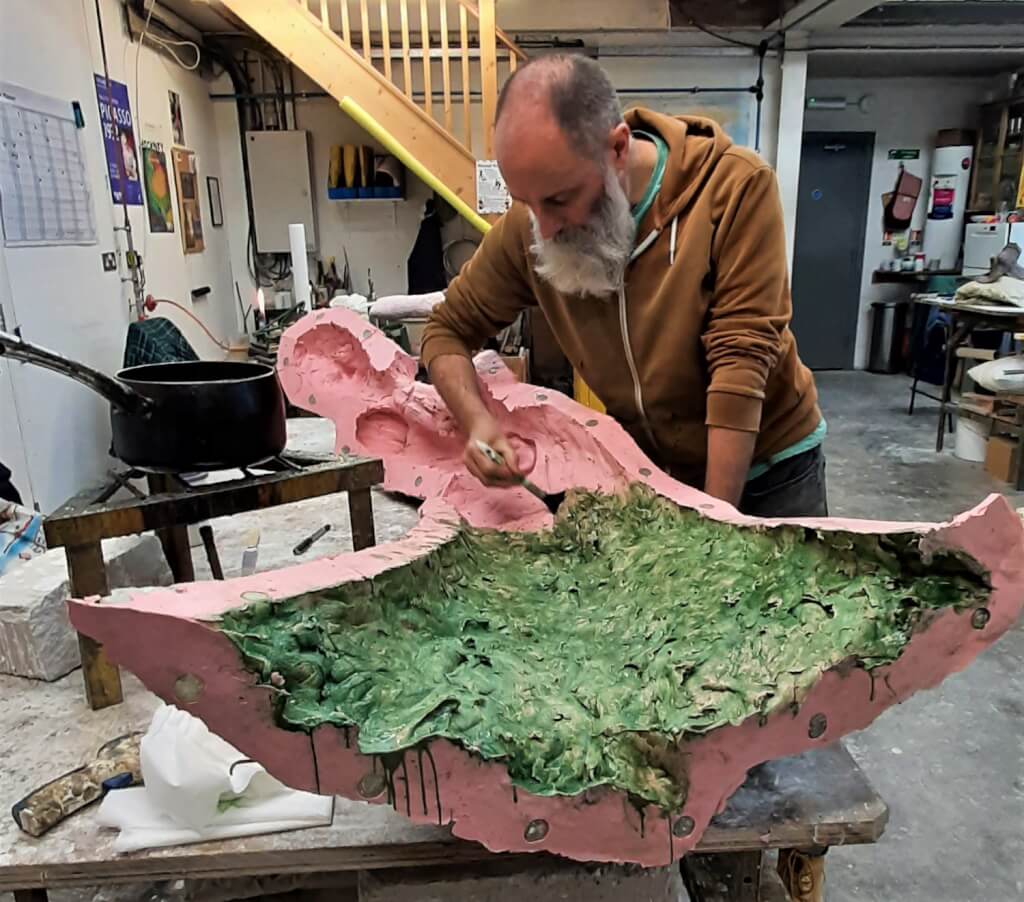
Here is one section of the mould being painted with molten wax. The wax is exactly where the bronze will end up!
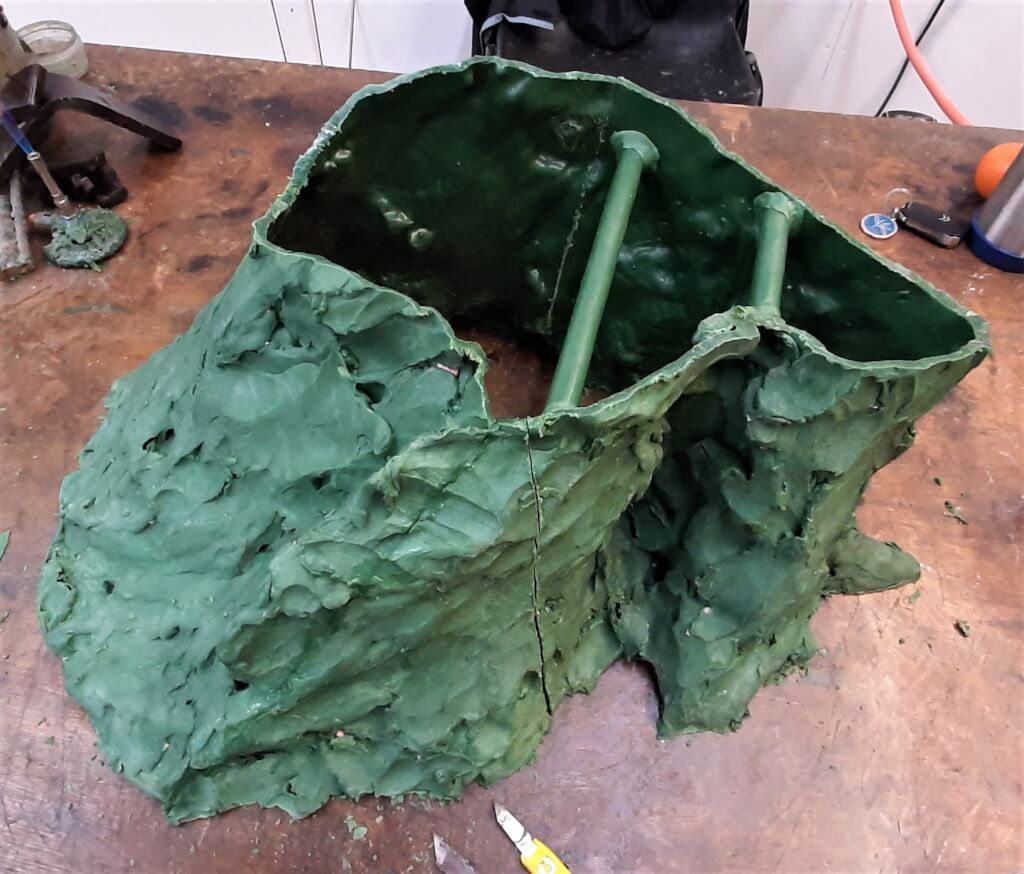
So here is the end of the first step. The bottom 600mm section of the casting has been formed out of wax. The circular rods are braces to hold the wax sections in place.
We’ll show you the various steps as we go along, so follow the blog and you can follow the process!
See the finished Speak to us of Freedom sculpture here.